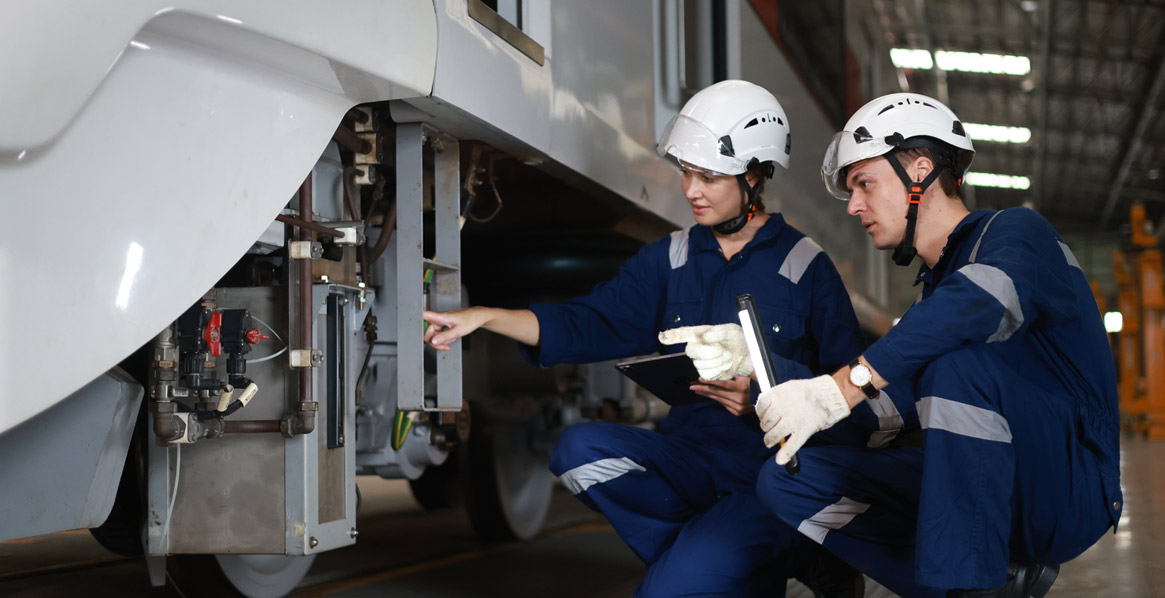
Predictive Maintenance on Rail Vehicles
With LUNA, LÜTZE TRANSPORTATION offers an intelligent and modular control system based on Ethernet TRDP and the local L-Bus2. It is designed for 2-pole switching, monitoring, and securing of 24 V actuators in rail vehicles. LUNA enables predictive fault forecasting and thus preventive maintenance.
For rail vehicle operators, the costs for maintenance and service of their vehicles are crucial for economic success and to remain competitive with other modes of transportation. Increasing system complexity, the challenging availability of spare parts—especially for older vehicles or specialized components—along with the shortage of skilled workers and high wage costs are significant price drivers. Consequently, manufacturers are required to offer maintenance and service options that ensure efficiency, reliability, and safety in rail transport.
In this context, "Predictive Maintenance," or proactive maintenance, plays a central role. This involves monitoring the condition of vehicle components through real-time data analysis, so that preventive maintenance can be performed at signs of wear before the component fails. This significantly reduces downtime.
The new LUNA system (Lütze Universal Network Adapter) from LÜTZE TRANSPORTATION implements such preventive maintenance, as demonstrated in applications within a modern dual-mode locomotive. The system enables continuous energy management based on the data collected through constant current monitoring. Sensor data is continuously analyzed to predict upcoming failures of consumers and to plan necessary maintenance in advance.
In addition to continuous current monitoring, LUNA offers remote on/off switching of all connected actuators via Ethernet TRDP. This allows LUNA to be installed in hard-to-reach locations and eliminates the need for additional relays or semiconductor switches for actuator switching.
The LUNA system is suitable for installation in the driver's cabin, in enclosed electrical operating areas, as well as in the passenger compartment. It is fully rail-compliant and meets the standards EN 50155, EN 50121-3-2, EN 50124-1, EN 61373, EMV06, EN 45545-2, as well as Regulation No. EMV 06 of the Federal Railway Authority. Thanks to EMV 06, which regulates electromagnetic compatibility in the railway environment, retrofits (retrofit) by the operator are possible.
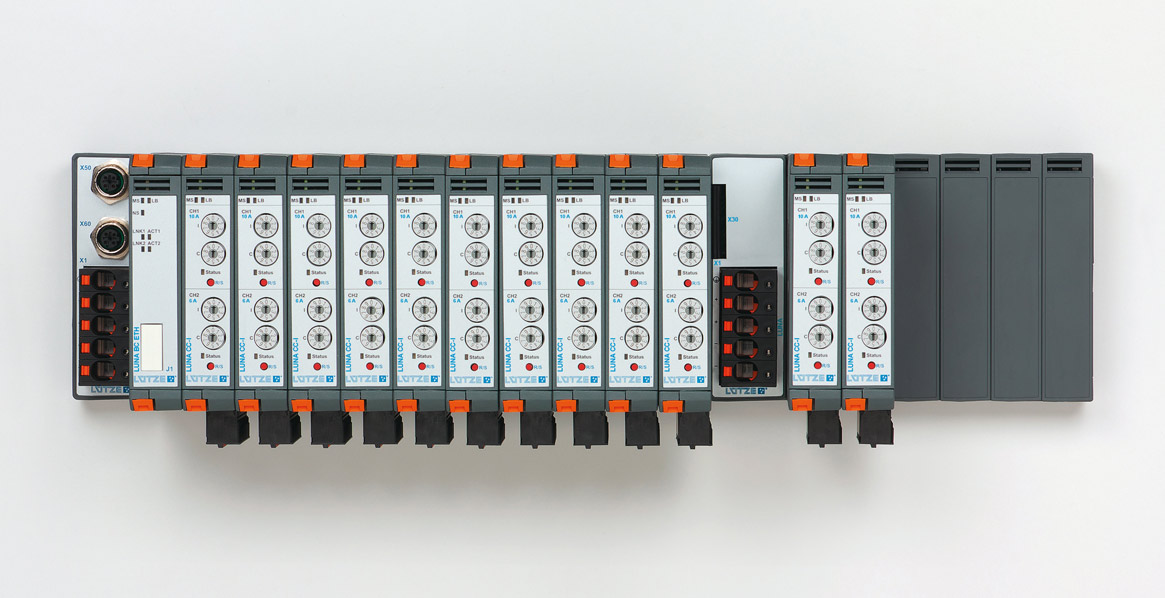
LUNA System Components - Power Supply and Expansion Modules
The LUNA compact power supply modules are functional units with 6 or 11 slots. The first slot is reserved for a bus coupler, while the remaining slots can be equipped with current monitoring modules. The system can be expanded with compact expansion modules (6 or 11 slots for current monitoring modules) to a maximum of 32 current monitoring modules. The expansion modules need to be supplied separately, while internal communication is passed through the L-Bus2.
With the LUNA power supply and expansion modules, LÜTZE TRANSPORTATION has developed rail-compliant compact units that significantly differ from conventional industrial plug-in housings. The LUNA system does not require data bridges or power bridges, simplifying installation considerably. Conventional plug connections often cause transition resistances that can reduce the supply currents. Since the LUNA system does not use these additional plug connections, supply currents of up to 100 A per power supply or expansion module are possible.
LUNA System Components - Current Monitoring and Protection Modules
The LUNA protection modules are characterized by their compact width of 22.5 mm, allowing for space-saving installation. Unlike many comparable industrial systems, the modules are designed with two channels. This means that two load monitoring units are built into one housing, which disconnects in a two-pole galvanically isolated manner in case of a fault or overcurrent: First, a transistor interrupts the current flow in the positive path. Then, a relay contact in both the positive and negative branches opens, ensuring a 2-pole, galvanically isolated disconnection.
In comparable industrial systems without galvanic isolation, where only a transistor disconnects, leakage currents can occur that continue to flow through the transistor. While these leakage currents are usually very small, they can cause significant problems in fully grounded networks (TN systems) and IT networks (isolated grounding systems). In TN systems, leakage currents can cause residual current devices (RCDs) or circuit breakers (MCBs) to trip even if no dangerous fault current is flowing. In IT systems, small leakage currents could affect insulation monitoring and make fault detection more difficult.
For the protection modules, extremely precise and realistic characteristics have been developed: quick, medium, slow 1, slow 2, and slow 3. These five characteristic curves have been electronically replicated and show significantly fewer tolerances than idealized curves based on magnetic or thermal principles. A disadvantage of the thermal principle is that the disconnection behavior can vary significantly between a cold and a warm circuit breaker. In rail applications, where large temperature fluctuations occur, this is particularly problematic. The electronically replicated characteristics of LÜTZE Transportation offer a much more reliable and consistent performance.
The electronic LUNA load monitoring units are available in three variants:
- Adjustable current range DC 1 A – 6 A | Channel 1: DC 6 A; Channel 2: DC 6 A
- Adjustable current range DC 1 A – 10 A | Channel 1: DC 10 A; Channel 2: DC 6 A
- Adjustable current range DC 1 A – 10 A | Channel 1: DC 10 A; Channel 2: DC 10 A
All load monitoring modules feature a permanently installed fuse in the positive and negative paths to ensure line protection in case of electronic failure. The 6 A channels are protected with a 10 A fuse, and the 10 A channels are protected with a 15 A fuse. The cross-sections of the connected cables must be designed to match the tripping current of these backup fuses.
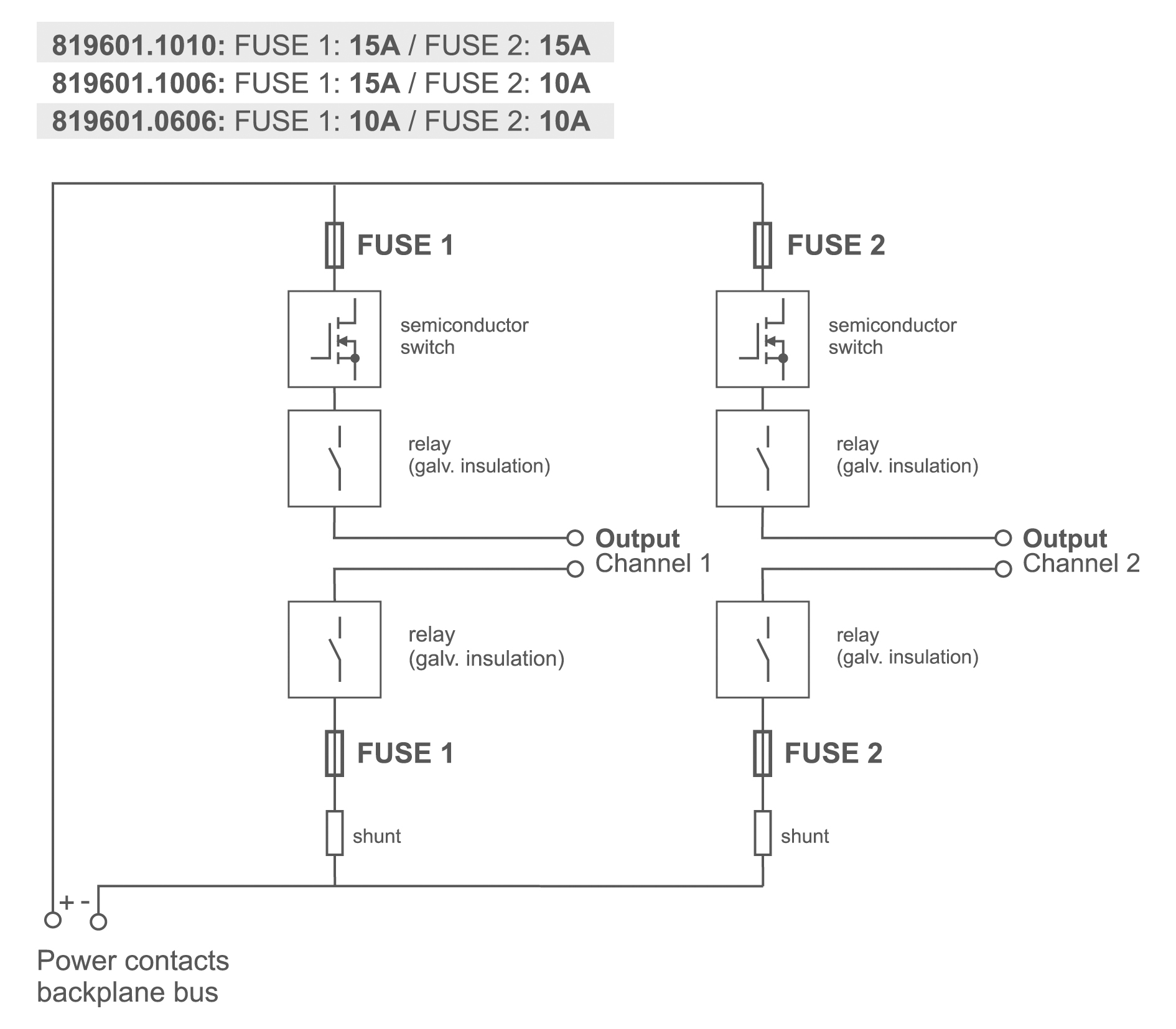
LUNA System Components - TRDP Bus Coupler
The LUNA TRDP bus coupler with a rear-wall bus L-Bus2 is installed in the first slot of the power supply modules. Up to 32 load monitoring modules (Devices) can be connected. Due to the modular design, connection to other fieldbuses is also optionally possible.
Application example in a Dual-Mode Locomotive - A system with four functions
The use of LUNA in a modern dual-mode locomotive for freight transport exemplifies the possibilities of the LUNA system. The vehicle combines the characteristics of a mainline locomotive with those of a shunting locomotive, and currently offers three drive variants: overhead line + diesel, overhead line + battery, and battery + diesel. The LUNA system provides four functionalities on the locomotive:
- Protection and intelligent current monitoring
- Continuous current monitoring for "Predictive Maintenance
- Energy management
- Switching elements for consumers
The intelligent current monitoring reports deviations in load currents, disconnects in case of overload according to the chosen characteristic, and can be reactivated via the control system. Conventional fuses are integrated into the positive and negative paths to protect the wiring.
With the permanent current monitoring of the LUNA system, the condition of each connected consumer can be monitored. Maintenance forecasts can be made as part of "Predictive Maintenance". For example, an increased start-up current or a continuous increase in current in a motor may indicate potential bearing damage. Persistent changes in current and voltage allow conclusions about the condition of an actuator, enabling preventive maintenance to be carried out in a timely manner. This reduces the frequency of total failures and allows for long-term, cost-effective maintenance planning. Through the TRDP connection, monitoring data can also be sent to the vehicle manufacturer’s or operator's cloud for more in-depth analysis.
The LUNA system manages the energy of the DC 24 V onboard network of the dual-mode locomotive. In critical voltage states, a shutdown profile with various levels and priorities can be implemented. Consumers with comfort functions can be switched off first, while safety-related functions remain operational.
LUNA also acts as a digital output module to remotely switch consumers on and off. Electronic fuses control various consumers such as signal and driver’s cab lighting, step and gangway lighting, and window heating. This allows a combination of electronic protection and switching elements, eliminating the need for relays or semiconductor switches.
Background TRDP vs. MVB
LÜTZE TRANSPORTATION currently uses TRDP (Train Real-time Data Protocol) for LUNA because it can transmit a significantly larger amount of diagnostic data compared to MVB (Multifunction Vehicle Bus). Additionally, the number of addressable participants is limited with MVB. The central advantages of TRDP Ethernet over MVB are:
- Data Transfer Rate and Bandwidth: TRDP Ethernet offers higher data transfer rates and greater bandwidths from 100 Mbps to several Gbps, compared to MVB Ethernet, which typically provides up to 1.5 Mbps
- Flexibility and Scalability: The MVB fieldbus is less flexible and scalable than TRDP. TRDP-based networks are easily expandable and support a large number of devices and communication nodes.
- Network Topology: TRDP Ethernet supports various network topologies such as star, tree, and ring, allowing for more flexible network configurations than MVB, which is limited to a bus topology.
- Fault Tolerance and Reliability: TRDP Ethernet offers advanced mechanisms for error detection and correction compared to MVB, which increases reliability.
Characters: 11,184 incl. spaces from bottom of page
Authors: Andreas Schindler, Product Manager at LÜTZE Transportation, and Volker Nefzer, R&D Project Manager at Friedrich Lütze GmbH
Cover picture credits: Maintenance on a rail vehicle (istockphoto.de)